定量包装自动化生产线实训系统(工程型)
随着科学技术的迅猛发展,生产力水平不断提高,人们对降低劳动强度、改善工作环境日益重视起来。传统的包装方式已不适应现代生产和管理的要求,而以PLC为基础组成的自动包装生产线,控制系统简洁方便,自动化程度较高,可减轻工人劳动强度,极大地提高了生产力;并且通过增加重金属检测系统,保证了产品符合外贸指标的要求。
1系统的基本技术要求
(1)供袋、称重、装袋、缝包、输送、质检、批号打印等都实现自动控制;
(2)系统操作方便,数据便于录人、修改;
(3)对物料流量进行准确称量和控制,并再配以给料设备组成定量给料;
(4)设备运行可靠,故障率低,抗干扰能力强;
(5)减少粉尘,改善工作环境;
(6)设备改造成本低,有良好的节能措施,技术先进等。
2控制系统硬件设计
在包装过程中,自动完成称重、供袋、取袋、装袋、缝口、输送、金属检测、重量检测等多个动作,动作多,运动复杂,而所处工作环境恶劣(高温、振动、粉尘),这就要求控制系统具有很高的可靠性、良好的节能措施、很强的故障诊断能力,确保生产的稳定运行。由于包装生产线的各种控制为开关量,而目前流行的PLC具有结构小巧、运行速度高、通用性好、可靠性高等特点,非常适合于工业现场的高温、振动、粉尘等恶劣环境下的开关控制。所以选用PLC作为控制系统的核心部件。
(1)PLC的I/O口分配及选型
输入点与输入信号、输出点与输出控制是一一对应的。分配好后,按系统配置的通道与接点号,分配给每一个输入信号和输出信号,即进行编号。FX2N型PLC的输入/输出通道号采用自由配置、固定通道方式。输入输出继电器可自由选择,与输入点对应的即为输入继电器,与输出点对应的即为输出继电器。列出输入输出接口分配表如表1。
(2) PLC选型
表1 I/0接口分配
输入 |
输出 |
名称 |
X000 |
名称 |
接口 |
紧急停止 |
X001 |
称重结束 |
Y004 |
秤启动/停止 |
X002 |
蜂鸣器 |
Y005 |
大螺旋给料 |
X003 |
大螺旋给料 |
Y006 |
真空过载 |
X004 |
紧急停止 |
Y007 |
小螺旋给料 |
X005 |
排出信号 |
Y010 |
输送带过载 |
X006 |
真空机启动 |
Y011 |
A机定量 |
X007 |
小螺旋给料 |
Y012 |
B机定量 |
X010 |
断线故障 |
Y020 |
压力正常 |
X011 |
缝纫机启动 |
Y021 |
袋库检测 |
X012 |
断线计数解除 |
Y022 |
袋送入 |
X013 |
断线故障保持 |
Y023 |
取袋真空 |
X014 |
缝纫切刀 |
Y024 |
取袋上下 |
X016 |
取袋上升 |
Y025 |
取袋送入 |
X017 |
边夹爪开 |
Y026 |
开口闭端 |
X020 |
拍打 |
Y027 |
夹爪压力 |
X021 |
扩张漏斗开 |
Y030 |
开口开端 |
X022 |
开口开 |
Y031 |
开口真空 |
X023 |
取袋下降 |
Y032 |
整形开端 |
X024 |
取袋真空 |
Y033 |
横移扩张侧 |
X025 |
边夹爪闭 |
Y034 |
横移封口侧 |
X040 |
取袋送入 |
Y035 |
缝纫机启动 |
X041 |
开口闭 |
Y040 |
缝纫机停止 |
X042 |
开口真空 |
Y041 |
缝纫机袋检测 |
X043 |
夹爪闭 |
Y042 |
下游机械运转信号 |
X044 |
夹爪曲 |
Y043 |
缝纫机过载保护 |
X045 |
扩张漏斗开 |
Y044 |
触摸屏 |
X046 |
不良袋除去 |
Y045 |
螺旋过载 |
X047 |
底震上升 |
Y046 |
线少量 |
X050 |
触摸屏 |
Y047 |
断线检测 |
X051 |
横移扩张侧 |
Y050 |
重量检测 |
X052 |
模移缝口侧 |
Y051 |
金属检测 |
X000 |
整形闭 |
Y052 |
|
|
导入闭 |
Y053 |
|
|
重检剔除 |
Y054 |
|
|
重金属剔除 |
Y055 |
根据I/O点数对PLC选型,加上一定的点数裕量,并考虑到以后扩展的需要,选用日本三葵FX2N可编程控制器。
3自动包装系统工作过程
物料自储料斗进入包装秤的给料装置,通过粗、细给料,当秤斗中的物料重量达到最终设定值时,称重终端发出停止加料信号,待空中的飞料全部落入秤斗后此次称重循环结束,此时包装秤等待装袋机的投料信号。当自动装袋机完成上袋后,发出信号,使称重箱打开卸料翻门,向包装袋内投料,卸料后称重箱关闭翻门,装袋机张开夹袋器,包装袋通过夹口整形机和立袋输送机进入自动折边机,包装袋经折边后,进入缝口机,当设在缝口机旁边的光电开关检测到包装袋后,缝纫机开始工作,缝合包装袋,当包装袋离开缝纫机后,缝纫机停止,并自动切断缝合线。包装袋经过倒袋整形机进入金属检测机及重量复检机,如果检测不合格,在包装袋通过质检单元时将被别除,而合格的包装袋则顺利通过,再经喷墨打印机设备,将包装袋输送到码垛区。
4程序控制逻辑
(1)自动供袋控制逻辑
当吸袋电磁阀得电时,若吸袋真空阀达到设定值,吸盘吸住袋子上升,到上限位时,水平送袋,将袋子送至下料口下方,夹爪与开袋吸盘闭合,夹住袋子,完成吸袋操作,这个过程不断重复进行。
同时夹袋电磁阀得电,当夹袋真空阀达到设定值时,空袋子袋口被夹爪夹紧,这时缩口夹子向里收,开袋、抱袋张开。检测开袋真空和夹袋压力,如果没有夹住袋子或没有把袋口打开,缩口夹子则松开,开袋真空和夹袋压力断开,然后进行吹袋操作:如果通过加紧压力检测袋子被夹住,同时真空开袋把袋口确实打开,则关闭真空和压力装置,卸料门打开,进行装袋,否则把各个功能部件返回到其原来位置。装袋时,开口吸袋器不再吸着袋子,返回初始位置。流程图如图1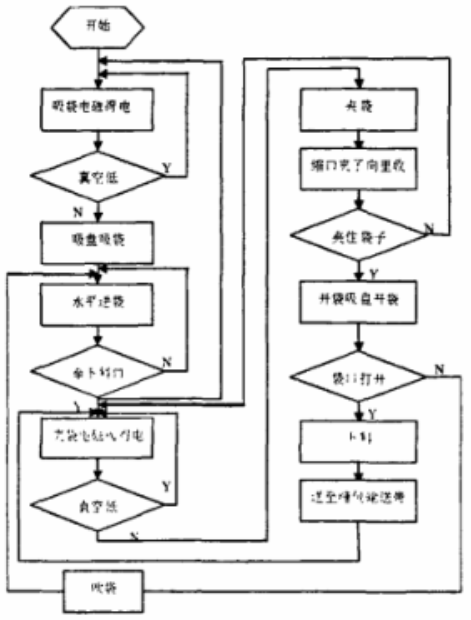
图1自动供袋流程图
(2)自动称重控制逻辑
当料仓破拱电机启动后,秤启动,螺旋给料机向称量斗里加料,大螺旋快速给料,当进料量达到预置重量的90%时,大螺旋给料机转为中速投料;当进料量达到预置总量的98%时,大螺旋停止给料,小螺旋开始细投料,当充填物料达到预置重量时,螺旋给料机停止给料,给料结束。检测到下面储料仓料已下净且无称料故障时,秤斗门打开放料;若检测到有称料故障,则进行人工放料。这个过程反复进行。自动称重流程图如图2所示。
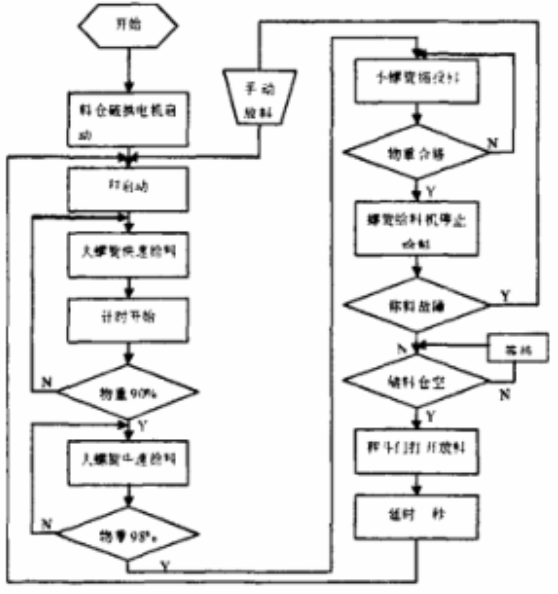
图2自动称重流程图
(3)自动装袋控制逻辑
袋口打开,从卸料门插入,然后秤卸料总定时器开始起动,总定时器的时间设定为装袋、拍打、敷实的时间.当定时到装料总时间的三分之二时,进行拍打,教实。总的定时时间到后,卸料门关闭,装料操作完毕,夹袋手爪将袋口绷紧,抱板与大夹子闭合送袋,夹袋松。自动装袋流程图如图3所示。
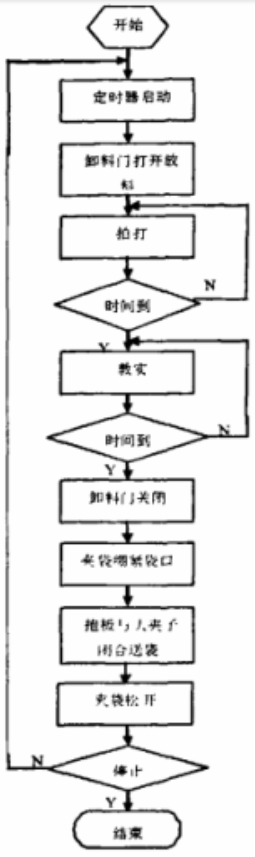
图3自动装袋流程图
(4)折边、缝口控制逻辑
当抱板与大夹子把装满料的袋子送到输送带上,完成夹送动作后,进行折边、缝袋口操作。此后重复上述各种操作。折边缝口流程图如图4所示。
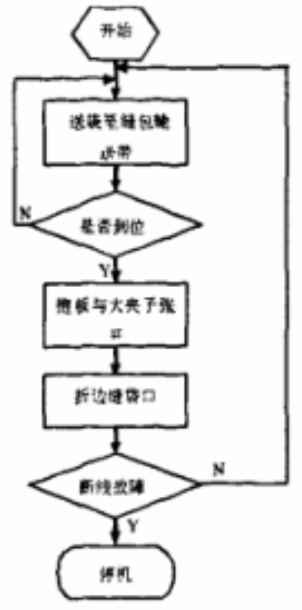
图4折边缝口流程图
(5) 倒袋、输送控制逻辑料袋由缝包机进入倒袋输送机,光电开关检测到科袋后,倒袋气缸伸出,将料袋推倒,进入整形部分,此后重复上述各种操作。倒袋、输送流程图如图5所示。
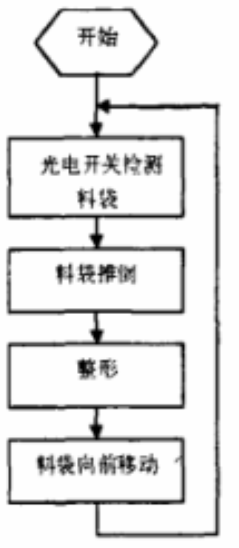
图5倒袋、输送流程图
(6)金属检测、重量检测控制逻辑
料袋通过金属检测输送机时,如果发现袋中有金属物体,检测器将发出警报,含金属料袋将由自动捡选机剔除。,合格料袋继续向前进入重量检测输送机,如果料袋重量不合格,也将由自动捡选机剔除。合格料袋继续向前输送。此过程反复进行。金属检测、重量检测流程图如图6所示。
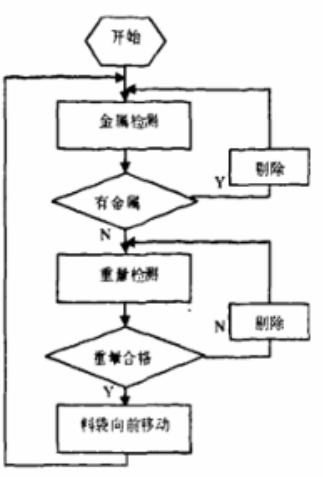
图6金属、重量检测流程图
6PLC程序设计
定量包装自动化生产线实训系统(工程型)是基于PLC集成控制的系统,根据以上叙述的内容中的系统整体控制流程图及系统的输人和输出信号,来编制PLC的梯形图。PLC采用循环扫描方式,按梯形图从上而下,从左而右的先后顺序予以执行。本程序使用了三菱公司全系列编程软件GX Developer Version8编辑。
7系统调试
在对系统硬件安装同时,首先对系统的程序进行在线仿真,通过仿真对程序调整,消去了一些多余的程序和不合理的程序,以减小扫描周期,发现程序设计中存在的问题。其次是对进行现场调试,单元调试、系统的整机调试、系统联运等。在进行调试的过程中,通过使用常见的故障的现象和原因去处理在设计过程中存在的问题,并分析解决的存在问题。对系统的测试及运行状况进行总结。
8结论
本项目的改造实现了自动化控制,采用国产化装置与进口设备相结合,在技术上可达到国内外先进水平,满足了设计要求,在投资上却远低于引进技术的装置。经过各方面工作人员的共同努力下,系统获得了比较好的应用效果。
相关信息